Inside Toyota’s $1.8B Factory of the Future That Can Build Anything
Toyota’s $1.8B K-flex overhaul transforms its Georgetown factory into the world’s most agile plant, ready for hybrids, EVs, and future mobility.
Toyota’s Georgetown plant just became the most flexible auto factory on the planet, capable of building hybrids, EVs, and anything else the market demands.
Georgetown, KY isn’t just where Camrys have long rolled off the line. It’s now the proving ground for Toyota’s K‑flex revolution. This $1.8 billion reinvention is about more than new models. It’s a future-proof factory, primed for next-generation mobility.
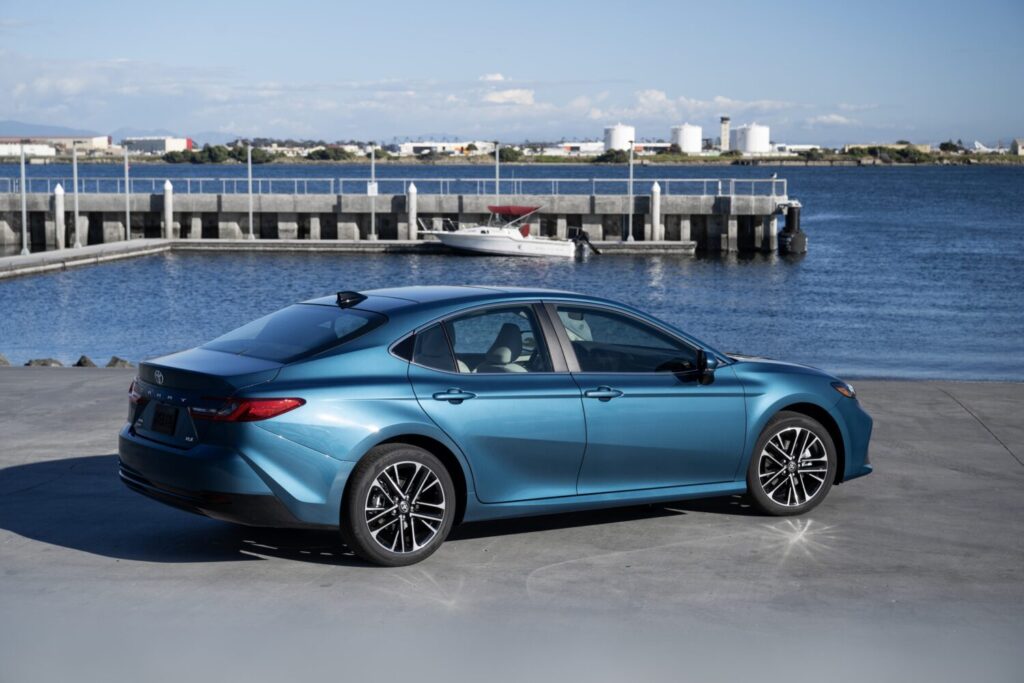
Why does this car matter right now?
Legacy automakers are scrambling as electric vehicle competitors surge. Toyota’s K‑flex, guided by autonomous robots, AI-driven material carts and a door-to-door chassis flow, transforms its Georgetown plant into what Toyota calls the most flexible automotive assembly line in the world. This isn’t a hypothetical transformation. It’s a tangible shift toward modular, tech-forward manufacturing.
How does it compare to rivals?
While other automakers still largely rely on fixed-line assembly, K‑flex introduces autonomous, rail-free skillets that reroute around obstacles and charge themselves as needed. The plant is equipped with advanced systems that streamline material handling and allow multiple vehicle types to be built on the same line. Toyota pairs that with new assembly line architecture that replaces the traditional nose-to-tail model with a more compact, responsive layout. It’s a leap ahead in operational agility.
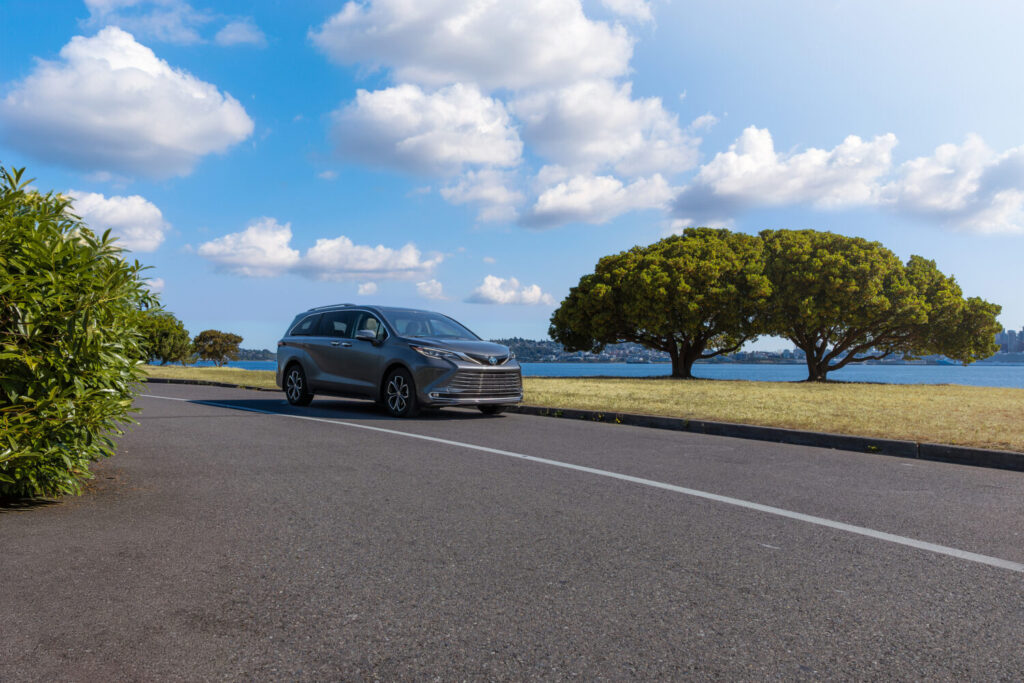
Who is this for and who should skip it?
This overhaul isn’t aimed at Camry or Highlander buyers directly. The real audience is Toyota’s engineers, investors, and internal operations teams. K‑flex allows the plant to seamlessly shift between building Camrys, Highlanders, plug-in hybrids, and fully electric vehicles without interrupting production. Consumers may not see the robots, but they’ll feel the impact in better availability, faster rollouts, and potentially lower costs. If you’re a buyer looking for flash, K‑flex isn’t the selling point. It’s the reason your new Toyota shows up on time.
What’s the long-term significance?
K‑flex signals Toyota’s pivot to full-spectrum manufacturing autonomy. The plant’s secure Wi-Fi backbone acts like a digital nervous system, connecting everything from assembly tools to parts delivery robots. This new system is expected to become the global template for Toyota manufacturing. The message is clear. Factories are no longer just buildings filled with people and machines. They’re intelligent, reconfigurable systems built to adapt as quickly as the market demands.
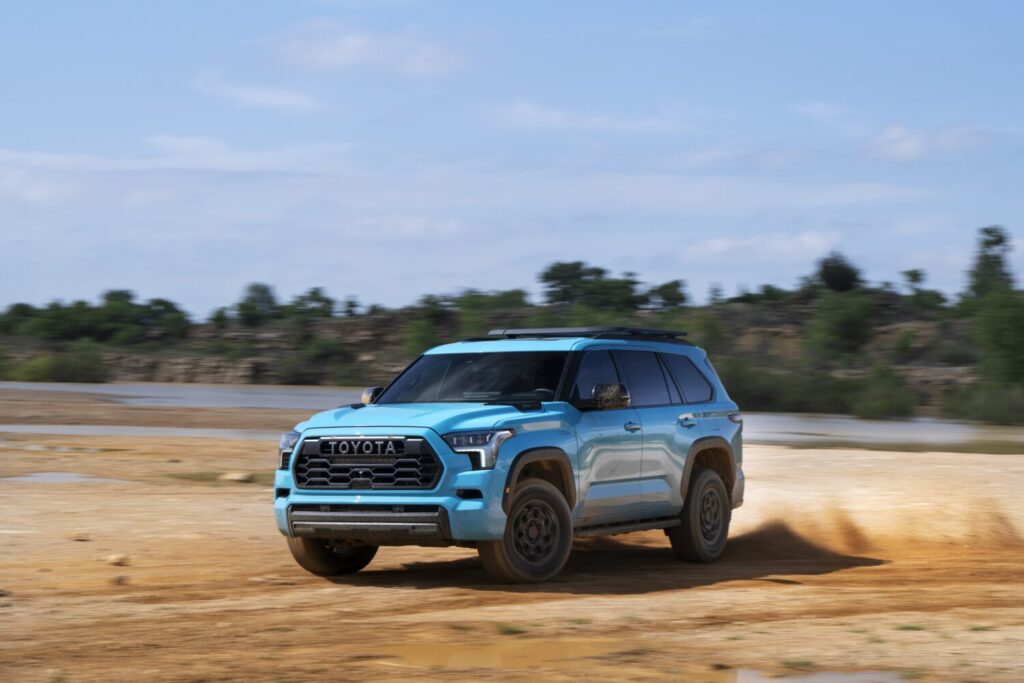
Specs, trims and pricing
The investment totals $1.8 billion. Output will include the existing Camry lineup, as well as future plug-in hybrid and fully electric models. The new production flexibility supports integration with upcoming battery supplies from Toyota’s North Carolina facility. Trim-level details remain under wraps, but the focus is on platform adaptability rather than just cosmetic variety.
On-the-ground perspective
Inside the Georgetown plant, you’ll see chassis moving side-to-side rather than front-to-back. Workers stay in place while smart systems bring the parts directly to them. The result is a quiet, almost choreographed precision. It feels less like an old-school assembly line and more like a well-rehearsed ballet of machines and humans working in sync. This is the kind of behind-the-scenes engineering that keeps Toyota a step ahead.
Toyota’s message is simple. The future isn’t waiting, and neither should the factories that build it. K‑flex is how they intend to lead.
Like what you’ve read? Stay in the driver’s seat with more insider automotive insights. Follow @NikJMiles and @TestMiles for stories that go beyond the press release.